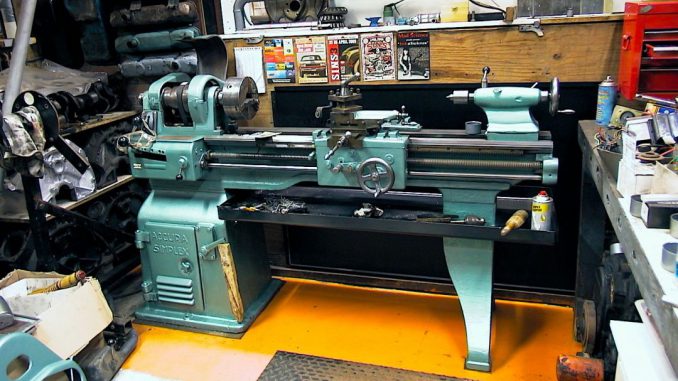
Was able to buy a lathe from a good friend for a good price. The fact that he even offered to drop it off at my place for free was more icing on the cake.
I’ve been wanting to own and be able to work with a lathe ever since childhood but it never happened. Until I stumbled on this one.
It’s an Empire Mondial / Accura Simplex lathe (6.5″ x 40″).
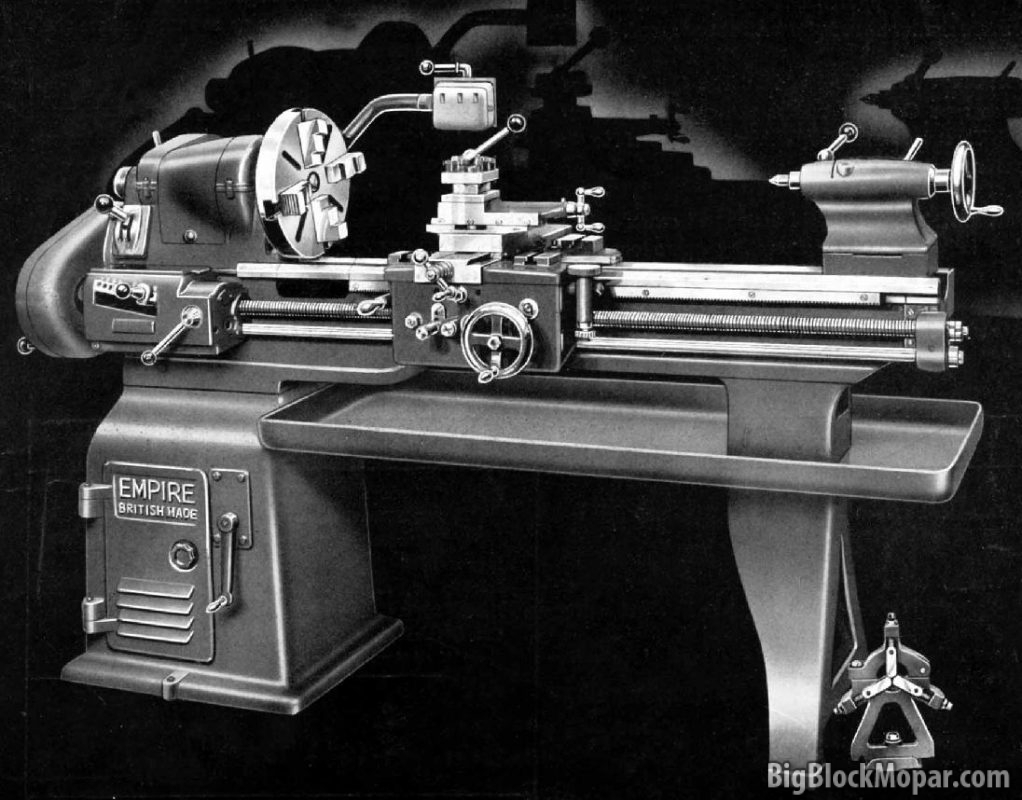
The Lathe was partly disassembled at my friends place for ease of transport. Upon arrival at my garage I deciced to take the opportunity to strip the old paint of the beast and apply a fresh new, old looking color.
I also was able to check and correct any worn parts and do some maintenance on most of the lathe parts.
After a good amount of scraping, sanding and repainting all the heavy parts, it was time reassemble the lathe.
As dissasembly was done quickly, reassembly took some more time but finally all the pieces were put in place again. Some with the help of my trusty engine-crane.
The original leather/cloth drive belt had stretched a bit since it was new. This caused it to slip and run off the pulleys whenever a little too much load was placed on it.
I thought I could replace it with an automotive serpentine multigroove belt in the same way the old belt was installed; by cutting it open and tying the ends together with hooks, or stitched soft steelwire.
Althoug it turned out the wiring pulled through the serpentine belt everytime as the belt was not capable of withstanding the weight and force of the electric drive motor for too long in the lower part of the lathe.
After some consideration I noticed that with some careful disassembly, it was possible to install a fully looped serpentine belt over the headstock and electric motor pulleys.
As a result the lathe ran much quiter than before and was able to put out more force again as opposed to the original belt.
The 3-jaw chuck had some trouble clamping and positioning a piece entirely straight so the idea was born to try and grind the jaws straight again.
Grinding was done with very little force but a multitude of passes were made. This worked quite nicely and got rid of 95% of the off-center issues. This simple operation with a Dremel gave some new life to the old chuck.
Leave a Reply